Understanding The Structure And Function Of A Laundry Machine Drum For Seo Optimization
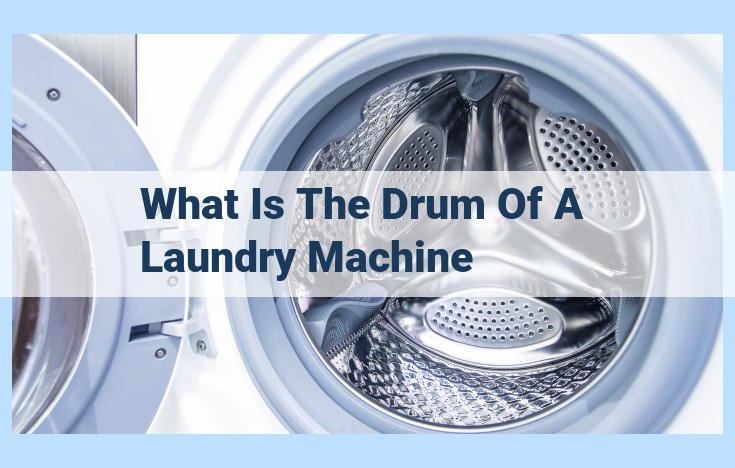
The drum of a laundry machine is a cylindrical chamber that houses the contents during the washing process. It comprises a drum body, baffles or lifters for agitating the contents, and bearings for smooth rotation. The drum rotates around a shaft, powered by a drive belt or motor. The tumble action of the rotating drum ensures thorough cleaning. Its size and capacity determine the volume of laundry it can accommodate. Perforations allow water flow and draining. Regular maintenance includes cleaning, descaling, and bearing replacement to ensure optimal performance.
Understanding the Essence of a Drum Body: A Gateway to its Functionality
The drum body, the heart of any rotary drum, stands as an unassuming yet crucial component. It’s the primary housing, the protective sanctuary for the contents within. Its shape and material hold the key to understanding its role and influence on the drum’s overall performance.
Shape and Design
The drum body’s shape is often cylindrical, providing ample room for the contents to move freely and interact with the drum’s internal mechanisms. In some cases, the body may adopt a conical or hexagonal shape, optimizing space utilization and specific process requirements.
Materials and Construction
The material chosen for the drum body hinges on the nature of the contents and the operating environment. Stainless steel, known for its corrosion resistance and durability, is a popular choice. Other materials, such as carbon steel, aluminum, and plastic composites, may be selected for their specific properties, such as strength, weight, or chemical compatibility.
Content Containment and Protection
The drum body’s primary function lies in housing and protecting the contents. Its seamless construction prevents leakage, ensuring that materials are kept safely within during the tumbling process. The strong material withstands the weight and forces exerted by the contents, maintaining structural integrity.
The drum body, despite its seemingly simple appearance, plays a pivotal role in the operation of a rotary drum. Its shape and material are carefully chosen to suit the specific application, ensuring the efficient containment and protection of the contents within. Understanding this component’s significance is crucial for optimizing drum performance and achieving desired process outcomes.
The Unsung Heroes of Drum Agitation: Baffles and Lifters
In the realm of industrial or commercial washing machines, drums play a crucial role in agitating and processing materials. Within these drums, baffles and lifters are unassuming yet indispensable components that silently work behind the scenes to ensure efficient cleaning and mixing.
Baffles: The Guardians of Turbulence
Baffles are stationary protrusions located inside the drum that create turbulence and agitation as the drum rotates. They come in various shapes and sizes, and their primary purpose is to lift and mix the contents within. This constant churning action prevents the formation of clumps and ensures uniform contact with the cleaning solution or mixture.
Lifters: The Gentle Giants of Dispersion
Lifters, on the other hand, are dynamic components that actively lift and move the contents upward. They are typically blade-shaped and attached to the drum’s interior. As the drum rotates, the lifters engage with the materials, creating a cascading effect that promotes dispersion and aeration. This gentle yet effective action helps separate and distribute the contents, improving cleaning efficiency.
The Intricate Dance of Agitation and Mixing
Together, baffles and lifters work in concert to create a carefully orchestrated turbulent flow within the drum. The baffles generate chaos and agitation, while the lifters use this turbulence to their advantage, lifting and tumbling the contents. This dynamic interplay ensures thorough mixing, prevents settling or clumping, and ultimately enhances the overall performance of the washing or mixing process.
While often overlooked, baffles and lifters are essential elements in the effective operation of industrial and commercial drums. Their ability to agitate and move the contents within the drum is a testament to their importance in achieving optimal cleaning or mixing results. By understanding the role of these unsung heroes, we can appreciate the intricacies behind the efficient operation of these powerful machines.
Bearings: Discuss their importance for smooth rotation and support.
Bearings: The Unsung Heroes of Smooth Drum Rotation
At the heart of every efficient drum machine lies a set of hidden heroes—bearings. These unsung components are essential for ensuring smooth rotation and providing reliable support to the drum as it performs its tireless duty.
The Role of Bearings
Bearings act as the interface between the drum shaft and the drum body, enabling the drum to rotate freely without any unwanted friction or resistance. They are strategically positioned to support the weight of the drum and its contents, ensuring that it rotates evenly and without wobbling.
Materials Matter
Bearings are typically crafted from durable materials like steel or ceramic, which can withstand the rigors of continuous rotation and heavy loads. These materials also possess excellent corrosion resistance, making them ideal for use in harsh environments.
Maintenance and Longevity
While bearings are designed to last, they require regular maintenance to ensure optimal performance. Periodic cleaning and lubrication help remove dirt and debris that can cause premature wear. Regularly monitoring bearing noise and vibration levels can help identify potential issues early on, allowing for timely replacement.
By understanding the crucial role played by bearings in drum operation, we can appreciate the importance of proper maintenance to ensure long-lasting performance and efficient mixing. So, the next time you hear the soft hum of a drum machine, remember the unsung heroes within—the bearings that tirelessly enable its smooth rotation.
The Central Axis of Rotation: Exploring the Drum’s Vital Shaft
Within the heart of every tumbling drum, lies a crucial component that ensures its smooth and efficient rotation: the shaft. Acting as a central axis, this cylindrical rod provides structural stability and facilitates seamless movement.
Think of the shaft as a dependable pillar, supporting the entire drum and its contents. Its strength and diameter play a pivotal role in determining the durability and load-bearing capacity of the machine. A robust shaft can withstand the rigors of continuous operation, preventing bending or breakage that could compromise performance.
The diameter of the shaft is equally important, as it determines the drum’s stability and rotation speed. A thicker shaft imparts greater strength and allows for increased rotational forces, while a thinner shaft facilitates faster speeds with reduced torque.
The precise engineering of the shaft ensures that the drum rotates smoothly and evenly, eliminating wobbling or uneven loading. This precision is essential for maintaining uniform agitation and achieving optimal results in various applications, such as industrial mixing, laundry operations, and food processing.
Exploring the Intricate Anatomy of a Dryer Drum
A clothes dryer drum, the heart of this household appliance, is a complex symphony of components working harmoniously to transform wet laundry into cozy, dry garments. Understanding the inner workings of this essential machine will empower you to maintain it with care and ensure its optimal performance.
At the core of the dryer’s drum assembly lies the shaft, a sturdy metal rod that serves as the central axis upon which the drum rotates. Its diameter and strength are meticulously engineered to withstand the constant tumbling action without succumbing to wear or breakage.
The drive belt or motor, the powerhouses of the dryer, provide the necessary force to rotate the drum. The drive belt, a thick, durable rubber or polyurethane band, encircles the drum and the motor pulley, transmitting power from the motor to the drum. Alternatively, some dryers employ a direct-drive motor that eliminates the need for a belt, offering greater efficiency and longer durability.
The motor, a compact but mighty electrical component, converts electrical energy into mechanical energy, enabling the drum to rotate. Its power output is cleverly tailored to the capacity of the dryer, ensuring efficient tumbling and effective drying.
Additional Resources:
The Enigmatic Tumble: How the Drum’s Movement Transforms Contents
The heart of any tumbling machine lies in its ability to agitate and move contents with precision. For example, the washing machine’s drum performs a mesmerizing dance during its cycles, playing a pivotal role in cleaning and refreshing your garments.
As the drum rotates, it creates a unique tumble action. This action simulates the gentle kneading and swishing motion of handwashing, effectively lifting dirt and grime from fabrics without damaging delicate fibers.
The tumble pattern varies depending on the machine’s design. Some drums rotate in a circular motion, while others employ a more complex figure-eight or spiral movement. This variation in movement ensures that all areas of the fabric receive equal attention.
The tumble action is also crucial for distributing detergent and cleaning agents throughout the contents. As the drum rotates, the liquid is lifted and sprayed onto the fabrics, penetrating deeply into the fibers to remove stains and odors.
Moreover, the tumble action promotes aeration, allowing fresh water to circulate through the load and remove dissolved dirt. This continuous rinsing helps eliminate detergent residue and ensures that your clothes emerge fresh, clean, and revitalized.
Capacity and Size: Explain the size and volume of the drum, and how it relates to the volume of contents.
The Capacity and Size of a Drum: A Vital Aspect
The capacity and size of a rotating drum are crucial factors influencing its performance and suitability for various applications. The drum’s size determines the volume of contents it can accommodate, which directly impacts the efficiency and productivity of the process. A larger drum allows for a higher volume of materials, leading to increased processing capacity.
For example, in industrial mixing, a larger drum enables the handling of larger batches, reducing downtime and increasing output. Conversely, in laundry applications, a smaller drum may be preferred for delicate fabrics that require a specific volume to move freely and prevent damage.
The drum’s size also affects its tumble action. Larger drums tend to have a gentler tumble, while smaller drums may have a more aggressive agitation, suitable for certain materials that require a more vigorous motion. The choice of drum size should therefore align with the specific requirements of the application.
When selecting a drum, it is essential to consider not only the volume of the contents but also the bulk density of the material. This refers to the mass of the material per unit volume. A higher bulk density indicates that the material is more compact, requiring a larger drum volume to accommodate the same weight of material.
By carefully considering the drum’s capacity and size relative to the volume and bulk density of the contents, businesses can optimize their processes, achieve maximum efficiency, and ensure the best results for their specific applications.
Perforations or Holes: The Secret Behind Effective Drying and Drainage
Perforations or strategically placed holes in the drum play a crucial role in ensuring efficient water flow and thorough drainage. These openings allow water to penetrate into the clothes, facilitating thorough cleansing.
During the tumbling process, the perforations create a suction effect. As the drum rotates, water is drawn through the holes, carrying away dirt and debris. This constant flow of water prevents the accumulation of water inside the drum, ensuring that clothes are rinsed and drained effectively.
Moreover, the perforations maximize air circulation within the drum. As the clothes tumble, air is drawn in through the holes, assisting in evaporation and promoting faster drying. This combination of water flow and airflow ensures that clothes emerge clean, fresh, and ready to wear.
The perforations in the drum are not mere design elements; they are essential for the proper functioning of a washing machine. By facilitating water flow, drainage, and air circulation, they play a crucial role in delivering clean, dry laundry every time.
Tumble Dryer Drums: A Comprehensive Guide to Components and Maintenance
1. Drum Components
Every tumble dryer has a drum that holds the laundry and tumbles it to remove moisture. The drum is typically made of stainless steel, which is durable and resistant to rust. It has a cylindrical shape to facilitate smooth tumbling.
Baffles, also known as lifters, are attached to the inside of the drum. Their main purpose is to agitate the laundry, ensuring even drying. They also help move the clothes from the bottom to the top of the drum, preventing tangling.
2. Rotation Mechanism
At the heart of the drum’s rotation is the shaft, a central axis made of sturdy steel. The shaft supports the drum and allows it to rotate smoothly.
Drive belts are used to power the rotation. They connect the motor to the shaft, transmitting the power that drives the drum. Some models may use a direct-drive motor instead of a belt, which eliminates the need for maintenance and reduces noise.
3. Drum Characteristics
The tumble action of the drum varies depending on the dryer model. Some drums rotate in a circular motion, while others oscillate from side to side. The tumble action helps distribute the laundry evenly and exposes all sides of the clothes to the heated air.
Capacity and size determine how much laundry the dryer can handle at once. The capacity is measured in cubic feet, and larger drums can accommodate more clothes.
Perforations or holes in the drum allow heated air to circulate through the laundry. They also allow moisture to escape, preventing it from condensing back onto the clothes.
4. Operational Aspects
Cleaning and Descaling
Regular cleaning and descaling are crucial for maintaining your dryer’s performance. Scaling occurs when minerals from the water accumulate on the drum and heating element, reducing efficiency and increasing energy consumption.
To clean and descale your dryer:
- Wipe down the drum: Use a damp cloth to remove any lint or debris from the drum.
- Run a vinegar cycle: Fill a cup with white vinegar and pour it into the drum. Run the dryer on the hottest setting for an hour without any clothes. The vinegar will dissolve mineral deposits and remove odors.
- Rinse the drum: Run a short cycle with just water to rinse away any remaining vinegar.
- Clean the lint filter: Remove the lint filter and wash it with warm soapy water. Make sure it is completely dry before reinstalling it.
By following these steps regularly, you can keep your dryer drum clean and scale-free, ensuring optimal drying performance.
The Crucial Role of Timely Bearing Replacement in Drum Maintenance
In the heart of a rotating drum lies a set of bearings, the unsung heroes that ensure smooth and efficient operation. These humble components play a pivotal role in supporting the drum’s weight and facilitating its rotation. Over time, however, bearings inevitably wear out, and their failure can lead to catastrophic consequences.
Consequences of Neglected Bearings
Neglecting bearing replacement is like playing a dangerous game with your drum. As bearings deteriorate, they can cause a myriad of issues that can compromise the integrity and performance of your equipment. Worn bearings generate excessive friction, which not only hinders rotation but also damages the shaft and other surrounding components. Overheated bearings can seize up, resulting in sudden equipment failure and costly downtime.
Preventive Maintenance: A Lifeline for Bearings
The key to avoiding these pitfalls lies in preventive maintenance. Regularly inspecting and replacing bearings before they reach the end of their lifespan is essential. By proactively addressing wear and tear, you can extend the life of your drum and prevent costly repairs down the road.
Signs of Impending Bearing Failure
Here’s how to spot the telltale signs that your bearings are clamoring for attention:
- Unusual noises: Grinding, screeching, or squealing sounds are often indicative of damaged or worn bearings.
- Excessive vibration: As bearings lose their ability to smoothly support the drum’s rotation, vibrations increase significantly.
- Overheating: Bearings that are nearing failure frequently run hot to the touch.
- Power consumption: Worn bearings require more energy to overcome the increased friction, leading to higher power consumption.
Replacing Bearings: A Skillful Intervention
Replacing bearings is a critical task that requires expertise and precision. The procedure involves carefully disassembling the drum, removing the old bearings, and installing new ones while ensuring proper alignment and lubrication. Attempting this repair without adequate knowledge can further damage your equipment, so it’s always advisable to entrust this task to qualified professionals.
By keeping a watchful eye on your drum’s bearings and replacing them promptly when needed, you’ll ensure that your equipment operates at its peak performance and avoids costly breakdowns. Remember, timely bearing replacement is not just a matter of routine maintenance; it’s an investment in the longevity and productivity of your drum.
Decoding the Secrets of a Drum’s Shaft: Troubleshooting and Repair Insights
Nestled within the heart of a drum lies a crucial component that orchestrates its rhythmic dance: the shaft. This unsung hero serves as the central axis around which the drum rotates, enabling it to perform its mesmerizing choreography. However, even the most steadfast shafts can encounter challenges that disrupt the harmony. In this chapter of our drum anatomy exploration, we’ll delve into the potential issues and ingenious shaft repair techniques that restore a drum’s smooth operation.
Bent or Warped Shaft: A Wobbly Predicament
Picture this: a drum struggling to maintain its graceful spin due to a bent or warped shaft. This misalignment can stem from excessive force, accidental impact, or prolonged wear and tear. The consequences are evident in a wobbly rotation, accompanied by an unsettling cacophony of sounds. When faced with such a predicament, expert repair becomes paramount.
Shaft Corrosion: A Silent Enemy
Corrosion, the insidious foe of metal, can also wreak havoc on a drum’s shaft. Moisture, acidic environments, or improper storage can foster this electrochemical process, leading to rust and premature shaft failure. The result is a compromised rotation and diminished drum performance. To combat this threat, regular inspections, proper lubrication, and protection from harsh conditions are essential.
Wear and Tear: The Inevitable Aging Process
As drums diligently fulfill their purpose, the shaft undergoes constant friction and stress. Over time, wear and tear takes its toll, manifesting in worn-out or damaged shaft surfaces. This wear can impede rotation, leading to a decline in drum efficiency. Professional repairs or shaft replacements may be necessary to restore optimal performance.
Shaft Repair: A Symphony of Precision
Restoring a damaged shaft to its former glory requires a deft touch and specialized expertise. The nature of the repair depends on the extent and type of damage. In some cases, skilled technicians can employ advanced techniques such as straightening, re-machining, or welding to restore the shaft’s integrity. In more severe instances, shaft replacement may be necessary to ensure a flawless rotation.
Preventive Maintenance: A Drum’s Elixir of Life
To prolong the lifespan of a drum’s shaft and minimize the need for repairs, a proactive approach to preventive maintenance is essential. This includes regular lubrication, proper storage, and periodic inspections. By adhering to these simple yet effective practices, drum enthusiasts can prevent premature wear, corrosion, and misalignment, ensuring their beloved instruments continue to produce rhythmic magic for years to come.