Diy Cookie Cutter Creation: A Step-By-Step Guide For Sheet Metalworkers
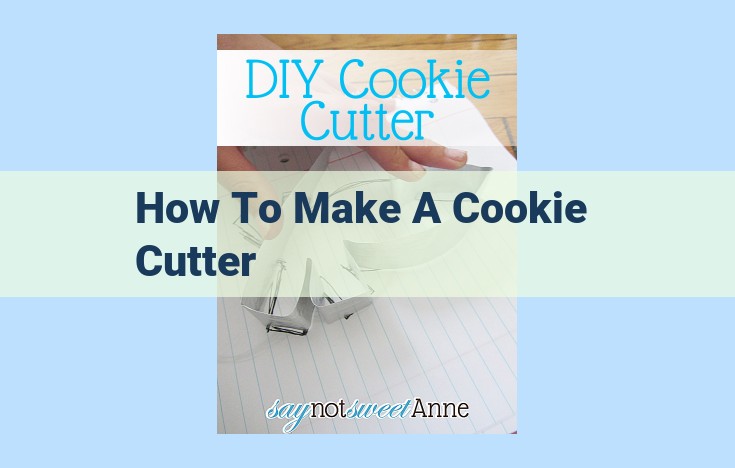
To create a cookie cutter using sheet metalworking, select a sheet metal type and measure the desired cutter shape. Use metal shears to cut the shape, then shape and refine the edges with a ball peen hammer. Secure the cutter to a solid surface with a metalworking vise. Use a soldering iron, solder, and flux to join the edges and create a seamless cutter.
Soldering Iron, Solder, and Flux: Discuss the types of soldering irons and their uses, as well as the importance of solder and flux in creating strong joints.
Soldering: A Vital Tool for Sheet Metalworking
In the realm of sheet metalworking, soldering stands as an essential technique for creating strong and reliable joints. This process involves joining two metal pieces using a metal alloy known as solder.
Types of Soldering Irons
The choice of soldering iron depends on the size and shape of the workpiece. For smaller projects, a pencil-tip soldering iron with a pointed tip provides precision and control. For larger surfaces, a fatter-tip soldering iron ensures even heat distribution.
Solder and Flux
Solder is the metal alloy used for joining metal pieces. It comes in various compositions, each designed for specific applications. Flux is a chemical agent applied to the workpiece before soldering. It removes oxides and impurities, ensuring a clean and strong bond.
The Soldering Process
- Prepare the workpiece: Clean the surfaces to be joined using sandpaper or a wire brush.
- Apply flux: Dab a small amount of flux onto the joint area.
- Heat the workpiece: Use the soldering iron to heat the joint until it reaches the melting point of the solder.
- Apply solder: Touch the solder to the joint and allow it to flow into the gap between the pieces.
- Allow to cool: Let the solder solidify to create a strong and durable bond.
Tips for Successful Soldering
- Use a clean and well-maintained soldering iron.
- Apply solder sparingly to avoid excess pooling.
- Hold the soldering iron perpendicular to the joint for maximum heat transfer.
- Don’t overheat the workpiece to prevent damage.
- Allow the joint to cool naturally to avoid cracking.
Delve into the Art of Metal Cutting: Essential Tools and Techniques
Step into the realm of sheet metalworking, where precision and craftsmanship intertwine. One crucial aspect of this meticulous process is metal cutting. Let’s explore the essential tools and techniques that enable us to transform raw sheet metal into intricate shapes and structures.
Sheet Metal: A Diverse Canvas for Your Creations
Sheet metal, the versatile foundation for countless projects, comes in a dazzling array of types and properties. From sturdy aluminum to pliable copper and resilient galvanized steel, each material offers unique characteristics that cater to specific applications. Understanding these properties is paramount to selecting the perfect sheet metal for your endeavors.
Scissors: A Deft Approach for Precision Cutting
For intricate cuts, specialized scissors come to the forefront. Aviation snips, with their long, straight blades, excel in making precise, straight cuts. Miter snips, on the other hand, are designed for angled cuts, allowing you to create crisp, clean joints. And don’t forget about compound snips, the versatile all-rounders that can tackle both straight and curved cuts with ease.
Tin Snips and Metal Shears: Power and Versatility for Demanding Cuts
When thicker sheet metal demands more muscle, tin snips and metal shears step up to the challenge. Tin snips, with their sharp, offset blades, provide excellent leverage for cutting curves and intricate shapes. Metal shears, true to their name, deliver exceptional power to effortlessly slice through even the most robust materials. Proper technique is key to prevent any mishaps, so always ensure a firm grip and proper alignment for clean, burr-free cuts.
Sheet Metalworking: Essential Tools and Related Trades
Sheet metalworking is an essential skill in various industries, allowing professionals to create intricate and functional objects from sheets of metal. At its core, it involves specialized tools and techniques to manipulate and shape metal into desired forms.
Essential Tools
Soldering Iron, Solder, and Flux: These tools are indispensable for joining sheet metal pieces together. Soldering involves using a heating tool to melt solder, a metal alloy, which then flows into the gaps between the metal joints. Flux aids in this process by removing impurities and ensuring a strong bond.
Metal Cutting
Various tools are used for cutting sheet metal:
-
Shears: These heavy-duty scissors come in hand-operated and powered versions. They are ideal for straight cuts, and their sturdy blades can handle different thicknesses of sheet metal.
-
Tin Snips or Metal Shears: These handheld tools look like large scissors and are specifically designed for cutting sheet metal. They are versatile and can make both straight and curved cuts.
Metalworking Tools
Additional tools are crucial for shaping and working with sheet metal:
-
Metalworking Vise: This tool holds workpieces securely in place, allowing for precise shaping and cutting.
-
Ball Peen Hammer: Its rounded head is used for shaping and forming metal through controlled hammering.
-
Anvil or Solid Surface: A solid surface provides a stable base for metalworking operations and protects tools from damage.
Related Skills and Trades
Sheet metalworking encompasses specialized trades that involve working with metal:
-
Metalworking: A broad field involving various techniques such as cutting, welding, and machining to create metal objects.
-
Tinsmith: A skilled tradesperson who specializes in working with sheet metal to create objects ranging from roofing to cookware.
-
Metalworker: A general term for individuals who work with metal in various capacities, including forging, welding, and fabrication.
Scissors for Sheet Metal: A Guide to Essential Tools
In the realm of sheet metalworking, where precision and finesse reign supreme, the humble scissor emerges as an indispensable tool. Its sharp blades and ergonomic designs make it an essential companion for those seeking to master this intricate craft.
Types of Shears for Sheet Metal
The world of sheet metal shears is a diverse one, each type boasting unique advantages suited to specific tasks. Here are the most common types:
- Aviation Snips: These lightweight and versatile shears are ideal for intricate cuts and tight spaces. Their curved blades allow for smooth curves and precise angles.
- Straight Snips: True to their name, straight snips excel at making straight cuts along long edges. Their larger size and robust blades provide extra leverage for clean and effortless cutting.
- Compound Snips: These powerful snips combine the cutting capabilities of both aviation and straight snips. Their offset blades provide excellent control for both straight and curved cuts.
Benefits of Using Shears for Sheet Metal
- Precision Cuts: Shears offer unparalleled precision, allowing you to execute intricate cuts with ease.
- Clean Edges: The sharp blades of shears create clean, burr-free edges, reducing the need for further finishing.
- Portability: Shears are lightweight and portable, making them ideal for both workshop and on-site work.
- Versatility: The variety of shears available ensures a perfect tool for any sheet metalworking project, from intricate crafts to large-scale fabrication.
Safety Considerations When Using Shears
- Sharp Blades: Always wear gloves to protect your hands from the sharp blades.
- Secure Workpiece: Ensure the sheet metal is securely clamped or held to prevent slipping and injury.
- Eye Protection: Wear safety glasses to protect your eyes from flying metal fragments.
- Proper Storage: Store shears in their designated holder to prevent accidental cuts and damage.
Mastering the art of sheet metalworking requires the right tools, and shears are an essential component of any tool kit. Their diverse types, benefits, and safety considerations make them an indispensable companion for any sheet metalworking enthusiast. So, whether you’re a seasoned pro or just starting your journey, embrace the power of shears and elevate your metalworking skills to new heights.
Tin Snips and Metal Shears: The Essential Tools for Precise Sheet Metal Cutting
When it comes to sheet metalworking, the right tools can make all the difference. Tin snips and metal shears are two indispensable tools for cutting sheet metal with precision and efficiency. These versatile tools offer a range of benefits that make them ideal for both professional and hobbyist metalworkers.
Tin Snips: The Compact Cutters
Tin snips are a compact and lightweight tool specifically designed for cutting thin sheet metal. They come in various sizes and styles, each suited for specific cutting tasks. Their short, angled blades provide excellent maneuverability and allow for precise cuts even in tight spaces. Tin snips are particularly useful for cutting curves and intricate shapes, as their blades can pivot and follow the desired shape.
Metal Shears: The Heavier-Duty Option
Metal shears, also known as aviation shears, are designed for cutting thicker sheet metal and heavier-gauge materials. These tools feature longer blades and a more robust construction, providing greater leverage and cutting power. They come with various blade lengths and thicknesses to accommodate different cutting requirements. Metal shears excel in straight-line cuts and can handle thicker materials with ease.
Advantages of Using Tin Snips and Metal Shears
- Precise Cuts: Both tin snips and metal shears offer precise cuts, minimizing burrs and distortions in the metal. This is crucial for creating clean and professional-looking results.
- Versatility: These tools can cut various sheet metals, including steel, aluminum, copper, and stainless steel. They are also suitable for cutting plastic, leather, and other non-metallic materials.
- Safety: Tin snips and metal shears are relatively safe tools when used properly. They feature ergonomic handles for comfort and grip, reducing fatigue and potential injuries.
- Ease of Use: These tools are straightforward to operate, making them suitable for both experienced craftsmen and beginners.
Techniques for Using Tin Snips and Metal Shears
- Proper Holding: Hold the snips or shears firmly with one hand while using the other hand to guide the workpiece.
- Blade Lubrication: Lubricating the blades with a light oil or grease can prevent binding and ensure smooth cutting.
- Cutting Direction: Always cut in the direction away from your body to avoid injury.
- Short Cuts: Make short, repeated cuts to avoid overloading the tool and damaging the blades.
- Support the Workpiece: Support the metal securely to prevent bending or distortion during cutting.
By mastering the techniques of using tin snips and metal shears, you can achieve precise, clean cuts in sheet metal, unlocking your creativity and enhancing your metalworking projects.
Metalworking:
- Metalworking Vise: Explain the purpose and types of metalworking vises, and how to properly secure workpieces for efficient metalworking.
- Ball Peen Hammer: Describe the uses and benefits of a ball peen hammer for shaping and forming metal.
- Anvil or Solid Surface: Discuss the importance of using a solid surface to support metalworking operations and protect tools.
Metalworking: Essential Tools in the Crafting Symphony
In the realm of metalworking, precision and skill dance together to create masterpieces from raw materials. Among the essential tools that orchestrate this transformative process are the metalworking vise, the ball peen hammer, and a solid surface (anvil or similar).
The metalworking vise, a steadfast companion in the workshop, grips workpieces with an unyielding grasp, ensuring they remain secure and stable during delicate operations. Different types of vises cater to specific tasks, such as swivel vises that allow for effortless positioning and bench vises that provide unwavering support. Mastering the art of securing workpieces is crucial for both safety and efficiency.
The ball peen hammer, with its distinctive rounded end, plays a versatile role in shaping and forming metal. Its gentle yet effective blows create subtle curves and contours, breathing life into cold, unyielding material. The hammer’s dual-purpose head, with a smooth end and a peened end, extends its capabilities to include both precision strikes and texturizing surfaces.
An often-overlooked but indispensable component of the metalworking arsenal is a solid surface. Whether it be an anvil or a sturdy tabletop, this foundation supports the intricate dance of hammer and chisel, protecting both tools and workpieces from damage. By providing a stable base for metalworking operations, the solid surface ensures accurate and consistent results.
Together, these essential tools form a harmonious symphony, enabling metalworkers to weave their craftsmanship into tangible creations. From intricate jewelry to colossal structures, the metalworking vise, ball peen hammer, and solid surface empower artisans to transform raw metal into works of art and marvels of engineering.
Metalworking Vise: The Indispensable Fixture for Precise Metalworking
In the realm of sheet metalworking, the metalworking vise reigns supreme as an essential tool that enables precision and efficiency. This sturdy fixture secures workpieces firmly in place, allowing for a wide range of metalworking operations to be performed with unwavering stability.
Types of Metalworking Vises:
The world of metalworking vises is diverse, catering to various needs and applications. Bench vises are commonly used, clamping workpieces to a workbench. Pipe vises specialize in gripping cylindrical objects, while swivel vises offer adjustable angles for greater flexibility.
Proper Workpiece Securing:
Mastering the art of securing workpieces in a metalworking vise is paramount. Ensure that the jaws are clean and free from debris, which can compromise gripping strength. Adjust the jaw pressure based on the thickness and hardness of the workpiece to prevent distortion. Always position the workpiece centered within the vise to distribute clamping force evenly.
By adhering to these best practices, you can transform your metalworking vise from a mere tool into an indispensable asset that enhances the precision and efficiency of your metalworking endeavors.
Shaping and Forming Metal with a Ball Peen Hammer
In the realm of sheet metalworking, a ball peen hammer emerges as a versatile tool for shaping and forming metal with precision. Its unique design, featuring a ball-shaped head on one end and a flat or slightly convex head on the other, makes it an indispensable tool for artisans and craftsmen alike.
Imagine a skilled metalworker carefully selecting a ball peen hammer, its weight and size perfectly suited to the task at hand. With each strike, the ball-shaped head delivers a concentrated force that gently dimples the metal surface, creating subtle curves and contours. This technique is particularly effective for doming or rounding sheet metal, allowing for the creation of intricate shapes and seamless transitions.
The flat or slightly convex head of the hammer serves a distinct purpose. It flattens and smooths the metal surface, removing any irregularities or imperfections left by the ball-shaped head. This dual-functionality of the ball peen hammer makes it an indispensable tool for both shape-making and surface finishing.
When working with a ball peen hammer, proper technique is paramount. Holding the hammer with a firm grip and using controlled and precise strokes ensures that the metal is shaped with accuracy and finesse. The weight and size of the hammer should be carefully chosen to match the thickness and hardness of the metal being worked on.
Patience and practice are essential virtues when using a ball peen hammer. It takes time and experience to master the delicate balance between force and finesse, ensuring that the metal is shaped without causing distortion or damage. The results, however, are often breathtaking, as the metal takes on new forms, transformed by the skilled hands of the artisan.
The Mighty Anvil: A Solid Foundation for Sheet Metalworking
Every craftsman knows the vital role an anvil or solid surface plays in sheet metalworking. It’s the bedrock that supports your every stroke, protecting your tools and ensuring precision.
Picture yourself hammering a piece of sheet metal. Without a solid surface to counterbalance your force, the vibrations would rattle through your tools, compromising their lifespan and the quality of your work. The anvil, like a patient sentinel, absorbs these vibrations, maintaining a stable and secure foundation for your efforts.
Moreover, an anvil serves as a protective barrier for your tools. When you strike the metal, the force is distributed evenly across its surface, preventing damage to your hammer or other equipment. It’s a guardian of your tools, ensuring they remain sharp and true.
Beyond its practical benefits, an anvil holds a symbolic significance in sheet metalworking. It represents the solidity and resilience required in this craft. Just as an anvil endures the relentless hammering, so too must the craftsman weather the challenges of shaping metal.
In choosing an anvil, consider its weight and surface area. A heavier anvil will provide greater stability, while a larger surface area allows for more expansive work. Ensure the anvil has a flat surface to ensure even distribution of force.
Whether you’re a seasoned tinsmith or a budding metalworker, an anvil is an indispensable tool. It’s the foundation upon which you can shape and craft your creations, a silent partner in your pursuit of precision and excellence.
Metalworking: A Journey into the Art of Transforming Metal
Introduction
Step into the realm of metalworking, where molten metal dances and shapeshift, and the skilled hands of artisans mold it into objects of beauty and function. Metalworking is an ancient craft that has evolved over centuries, leaving behind a trove of techniques and tools that continue to inspire modern-day metalworkers.
Essential Tools for the Metalworking Apprentice
Every metalworker’s toolbox is a sanctuary of invaluable tools, each playing a crucial role in the transformation of raw metal into masterpieces.
Soldering: The Art of Joining Metals
The soldering iron, a magician’s wand in the world of metalworking, employs heat and solder (a metal alloy) to fuse two pieces of metal together. Solder acts as the glue, bonding the metal surfaces, while flux, an invisible ally, removes impurities and ensures a strong, durable bond.
Cutting through Metal: Precise Tools for Clean Edges
The shears and snips, like sharp-toothed predators, tackle the task of cutting metal with precision. Sheet metal, a versatile material, can be tamed by the nimble hands of these cutting tools, revealing clean edges that form the foundation of intricate metal creations.
Metalworking Vise: A Fixture of Control and Precision
The metalworking vise, like a steadfast guardian, securely holds the workpiece, providing a stable platform for shaping, cutting, and bending. Its jaws, unwavering in their grip, keep the metal in place, allowing for precise and efficient metalworking operations.
Ball Peen Hammer: A Sculptor’s Ally
The ball peen hammer, a versatile artist’s brush, transforms metal through the power of gentle taps. Its rounded face gently curves and shapes the metal, breathing life into objects with intricate contours and delicate details.
Anvil or Solid Surface: A Foundation for Forging
The anvil, an unyielding sentinel, serves as a solid foundation upon which metal is shaped and forged. Its sturdy surface provides the perfect base for metalworking, absorbing the force of hammering and supporting the metal as it transforms before the artisan’s eyes.
Metalworking Disciplines: A Symphony of Skills
The world of metalworking is a vast tapestry woven with a myriad of specialized skills and trades.
Tinsmith: Crafting Objects from Sheet Metal
Tinsmiths, masters of sheet metal, possess the ability to transform humble sheets of metal into an array of objects, from intricate roofing systems to delicate decorative pieces. Their skilled hands manipulate the metal, coaxing it into shapes and forms that serve both function and beauty.
Metalworker: A Jack of All Trades in the Realm of Metal
Metalworkers, the masters of their craft, command a comprehensive knowledge of metalworking techniques, encompassing cutting, shaping, welding, and finishing. They navigate the intricacies of various metals, understanding their properties and how to harness their potential to create objects of exceptional quality and durability.
Sheet Metalworking: Essential Tools and Related Trades
Tinsmith: The Master of Sheet Metal Magic
In the realm of sheet metalworking, tinsmiths stand as skilled artisans, wielding their knowledge and dexterity to transform ordinary metal sheets into extraordinary creations. These masters possess an intimate understanding of sheet metal’s properties and an array of specialized techniques that allow them to shape, mold, and craft objects with remarkable precision.
From the intricate detailing of architectural adornments to the functional components of household appliances, tinsmiths’ work is ubiquitous and often goes unnoticed. Yet, their expertise is essential in a wide range of industries, including construction, automotive, and manufacturing.
One of the hallmarks of a tinsmith’s craft is their ability to work with thin sheets of metal. These sheets come in a variety of materials, such as steel, aluminum, copper, and zinc, each with unique properties that influence the tinsmith’s approach. Using specialized tools, they meticulously cut, bend, and solder individual pieces together to create complex assemblies.
Soldering, a crucial aspect of tinsmithing, involves joining metal components using a molten metal alloy known as solder. Tinsmiths carefully apply heat to melt the solder, which then flows between the metal surfaces, forming a strong and durable bond. This technique allows them to create leak-proof seams and secure intricate joints.
Tinsmiths are also skilled in a variety of metalworking techniques, including cutting, shaping, and finishing. They employ a range of tools, such as shears, snips, and hammers, to precisely shape metal sheets into desired forms. Anvil or solid work surfaces provide a stable base for these operations, ensuring accuracy and preventing damage to tools.
In addition to their technical expertise, tinsmiths possess a keen eye for detail and a deep understanding of the materials they work with. They are adept at reading blueprints, following instructions, and troubleshooting problems to ensure the highest quality in their creations.
The Versatile World of Metalworking: Exploring Related Skills and Trades
In the vast realm of craftsmanship, metalworking stands as a towering testament to human ingenuity and the transformative power of shaping metals into countless creations. Beyond the essential tools discussed earlier, this multifaceted field encompasses a wide spectrum of related skills and trades, each with its unique expertise and artistry.
Metalworking
At the heart of metalworking lies the ability to manipulate and shape metals through various processes such as cutting, shaping, welding, and finishing. Metalworkers possess a deep understanding of the properties of different metals and employ a range of techniques to achieve precise cuts, intricate forms, and durable joints.
Tinsmith
A specialized branch within metalworking, tinsmithing focuses on the meticulous manipulation of sheet metal. Tinsmiths create a mesmerizing array of objects, from intricate roofing systems to decorative architectural accents. Their skills include cutting, forming, and soldering sheet metal, transforming it into functional and visually stunning creations.
Other Metalworking Trades
The broader field of metalworking extends far beyond these two trades, encompassing a diverse array of specialized disciplines that cater to various industries and applications.
-
Forging: The ancient art of forging involves heating and hammering metals to shape them into intricate masterpieces, such as tools, weapons, and decorative objects.
-
Welding: This essential skill involves joining pieces of metal using intense heat or pressure to create strong and durable structures. Welders are indispensable in construction, manufacturing, and repair industries.
-
Machining: Using precision machines, machinists transform raw metal stock into intricate components with precise tolerances. Their expertise lies in creating complex geometries and smooth surfaces, vital for industries ranging from aerospace to manufacturing.
-
Fabrication: This broad field encompasses the design, assembly, and construction of metal structures. Fabricators combine various metalworking techniques to create everything from bridges to storage tanks, showcasing their versatility and craftsmanship.